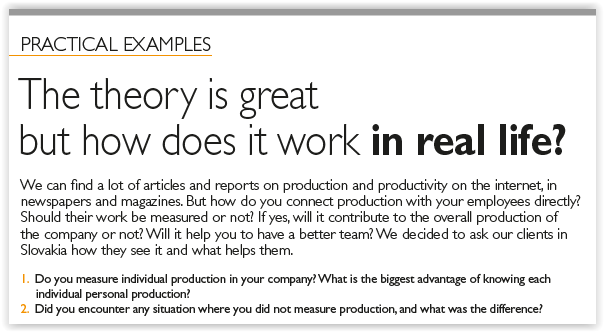
The theory is great but how does it work in real life?
We can find a lot of articles and reports on production and productivity on the internet, in newspapers and magazines. But how do you connect production with your employees directly? Should their work be measured or not? If yes, will it contribute to the overall production of the company or not? Will it help you to have a better team? We decided to ask our clients in Slovakia how they see it and what helps them.
- Do you measure individual production in your company? What is the biggest advantage of knowing each
individual personal production? - Did you encounter any situation where you did not measure production, and what was the difference?
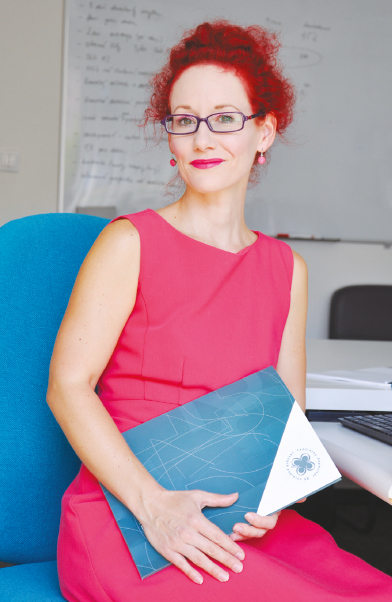
© L. Pazderová
Name: Mgr. Ľudmila Pazderová
Position: HR manager
Company: CDCP SR a.s. Slovakia
They measure individual production by statistics, which deflects fulfilment of the determined targets and production of the company. Each employee has within his job a description where the final result of the job is directly defined. Management sets the goals and standards for divisions, as well as for the whole company, and regularly monitors their fulfilment through key indicators in the graphs.
- The biggest advantage is the ability of management to respond immediately to fluctuations in efficiency and adopt flexible measures. But there are several other advantages:
■ clear overview of whether the products of the job and the employee are going up or down. This indicates in advance whether the company is expanding, stagnating or contracting.
■ direct connection to a reward system, which considerably influences motivation
■ better measurement of the effectivity, i.e. whether the results correspond with the amount of work assignments for the job and whether the workload corresponds with set requirements.
■ any sensible person enjoys self-motivation
■ visual quantification of results (stats, graph) is like a shield that an employee can use as an argument when discussing his production with his superiors. No assumptions, only facts. - Yes, we can see the difference. It is similar to driving a car without the dashboard. It is possible, but you do not know whether the engine is overheated, or you have enough petrol, or are staying within the speed limit or not. Before, we had a problem identifying weak and strong spots in our processes. We could not make decisions quickly and effectively, and we had a problem recovering from long-term losses. After implementing several important decisions, including the measurement of production, we showed more than 5 years of profit and got into a good condition.
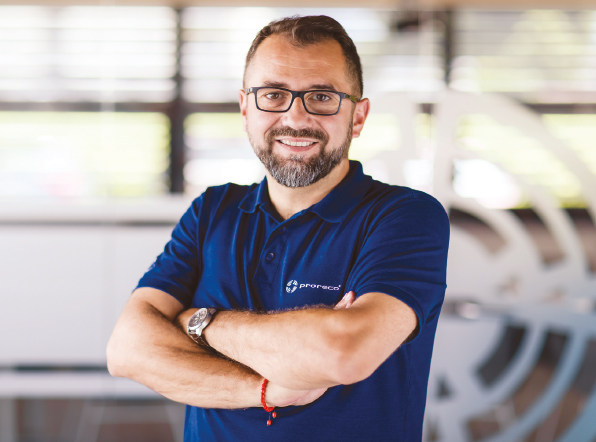
© M. Holenda
Name: Ing. Martin Holenda
Position: ED
Company: Proreco, Slovakia
They measure individual production in the company by assigning personal statistics to each employee.
- The main advantage is that we have factual data on the production of our employees, departments, and the whole company, and we can exactly determine the condition we are currently in. Because of the statistics, we have our company under control. The other advantage is that when we want to motivate and reward our employees, one part of the salary is connected to their personal statistics and thus to real production.
- The situation, before we implemented the stats, was a bit unrestrained; we were making decisions based on guessing rather than based on the actual facts. Of course, we had the data about production, but only the overall data, mainly based on our own production, accounting or sales records. Determining the trend was strenuous because we had to obtain the information from various sources, process and evaluate it. Now we have it faster, and the data are easy to get and thus the decisions are made faster.
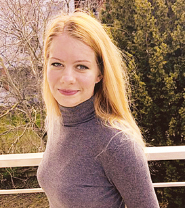
© L. Antalikova Archive
Name: Lucia Antalikova
Position: Owner
Company: ANT, Slovakia
They are a trading company and thus the production in sales is very easy to measure. If overall production is not following the targets, they immediately see which employee has a problem reaching his target and is causing the whole company to be behind schedule.
- The biggest advantage of knowing each individual personal production is that I can see whether the employee is managing his job or not. Whether he is contributing or is a burden for the company. Many times, production is the reason why the person was hired for that job, and thus the company should monitor their investment in this person. We monitor investment revenues on capital markets/stock markets, so why would we not do it with employees? On one hand we can see whether the person is an asset and, on the other hand, we can monitor his potential. In our company we have a natural pressure on production, because in a small company one position is closely following another, and people are “chasing” each other when one has a delay with delivering his or her product. We strictly make sure that sales targets are met in our company, which also creates a natural pressure to fulfill individual plans.
- We have measured individual production for a really long time and I, personally, do not recall a time when we did not. I could imagine that some companies operate without doing this, and I could assume that in bigger companies they do not have enough capacity to measure production for each individual. Such a situation could have two effects – either there is an individual holding the job who is not capable and nobody notices it, or there is a very capable person but because nobody measures his production, he goes by unnoticed whether he is producing a lot or a little. Not measuring production could discourage productive people, and for unproductive people it would be convenient. Our well-trodden path is to already start measuring production with each individual, continue with groups and up to the whole company. Our reward system is based on production as well.